Building the future of flight
Decades of experience, an innovative spirit: how we’re breaking barriers in propulsion
It sounds straightforward enough: Advanced propulsion is the art and science of moving people and things around the world, and the modern jet engine has made that possible.
But straightforward doesn’t mean “simple.” At least not in this case.
“The modern jet engine,” said Michael Winter, senior fellow for advanced technology at Pratt & Whitney, “is the most sophisticated mass-produced device known to humankind.”
It has more than 40,000 parts, some spinning at tens of thousands of revolutions per minute. At the front is a compressor that gets air so hot it could melt rocks. The compressed air flows into the combustion chamber, where it is mixed with liquid fuel and set afire, and the air-fuel mixture releases the heat energy that propels the plane.
But don’t try it at home. According to Winter, about 20 countries around the world can produce a nuclear weapon, but only a few can make a modern jet engine.
“This is a unique capability,” he said.
Advanced propulsion has also emerged as one of the most exciting areas for Raytheon Technologies, as the company’s engineers can draw on decades of experience, expertise, and research to forge breakthroughs in commercial aircraft, fighter jets, unmanned aerial vehicles and interceptors.
Making commercial flight more efficient – and more profitable
Since the dawn of the jet age in the 1930s, according to Winter, jet engines have improved in efficiency, on average, by 1 percent to 1.5 percent each year. That’s a testament to the researchers, engineers and companies that have sought continuous improvement, and it is a reminder of the many attributes, both real and latent, of propulsive technology: in both commercial and military use, the sky is indeed the limit.
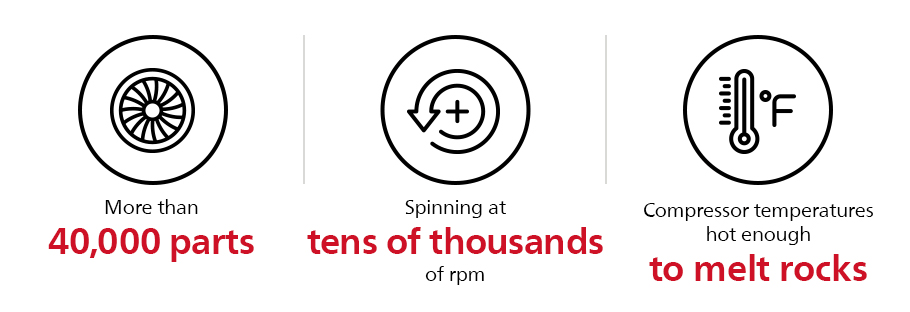
As much as any other factor, jet propulsion affects a commercial airline’s bottom line, as fuel represents 30 to 40 percent of the costs in running an airline. The more efficient the engine, the lower the costs, the greater the value. The story is much the same for military aviation, just without the profits: the more efficient the engine, the lower the cost of operations and greater the range.
Of course, commercial airlines worldwide have concerns beyond profitability.
In 2019, they burned just under 100 billion gallons of fuel, according to Winter, and that resulted in about 2.5 percent of carbon dioxide produced by all of humankind. By 2050, given the expected growth of global air travel (2020 notwithstanding), commercial aviation is expected to contribute just under 20 percent of greenhouse gas emissions, assuming there is no further intervention.
Not surprisingly, governments around the world are placing greater restrictions on emissions and noise, even as airlines are requiring that their planes travel even greater distances. That puts increased burdens on what propulsive technology can do now – and what it needs to do in the future.
Pratt & Whitney, a Raytheon Technologies business, has met such technical challenges before. In the 1960s, its J58 engine powered the SR-71 Blackbird reconnaissance jet, which was capable of flying faster than a rifle bullet. Then in 2016, it introduced the revolutionary Geared Turbofan engine, a $10 billion, 20-year investment that has a 16 percent lower fuel burn and a 50 percent lower output of oxides of nitrogen than its predecessor. It also has a 75 percent smaller noise footprint.
The lower fuel burn translates into reduced emissions of carbon dioxide of 3,600 tons per airplane per year.
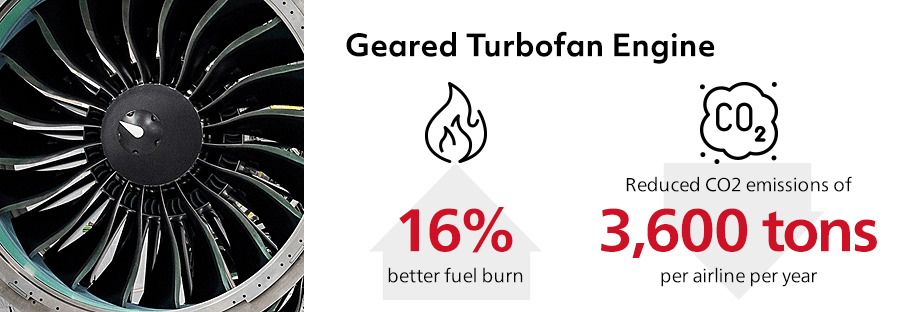
“Consider a tree in the forest,” Winter said. “The sun is shining, and the tree is doing photosynthesis. When that happens, it is pulling CO2 out of the air. In one year on a CO2 basis, one airplane [with a Geared Turbofan] is the equivalent of having 900,000 more trees.”
Pratt & Whitney and the Raytheon Technologies Research Center are working on the next generation of fuel efficiency improvements, which include more efficient fans, improved aerodynamics and higher-temperature materials. While battery technology remains relatively immature, Pratt & Whitney and the Research Center, working with Collins Aerospace, are developing hybrid electric solutions that will yield further improvements.
“The future is bright,” Winter said.
Supporting the military’s mission
The principals of propulsion technology are the same for the military – they just serve a different mission.
“From a military perspective, propulsion is about being able to get our warfighters where they need to be, when they need to be there, and then get them safely home,” said David Stagney, senior director at GATORWORKS, which is part of Pratt & Whitney Military Engines.
That has always been the goal, dating back to Pratt & Whitney’s aircraft engines that powered the Allies’ aircraft in World War II, but times have obviously changed. The military doesn’t want to, nor can it afford, to send 400 aircraft on a single mission to accomplish one objective, as it did in World War II.
Now it wants to deploy as few as possible to accomplish a mission – and to do so with precision and minimal cost, risk and collateral damage. Another big change is that all military aircraft once had at least one person on board. That’s no longer true, and it means engineers have to reconsider the design of the military aircraft, emphasizing the integration of its component parts.
The systems on a military aircraft – electrical, propulsion, and thermal management – have to work in harmony to achieve the best possible result.
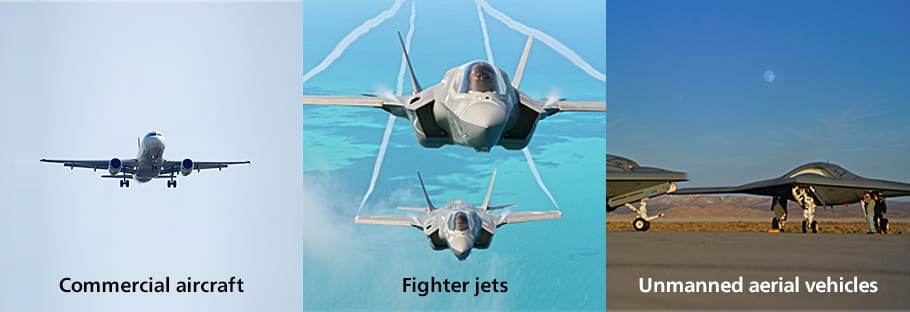
“If you only think about propulsion, you’re sub-optimizing what the vehicle is able to accomplish, because it’s not just about getting to the right place,” Stagney said. “It’s about being able to carry the right systems on board to accomplish a complicated mission and to protect the aircraft from whatever else is out there.”
The U.S. Department of Defense has challenged Pratt & Whitney to help rethink the overall capabilities of the vehicle, as opposed to the individual requirements for the engine.
“We’re taking a step back and looking at the mission that the customer wants to accomplish and offering solutions that you might not think about if you only considered the engine,” Stagney said.
The advent of unmanned flight has increased the types of missions that the military may deploy, which has increased the types of propulsion systems that need to be designed. Not having a human on board opens up options including more expendable engines that may last a few dozen missions, or sometimes just one.
“Rather than investing in spare parts, repair facilities, and mechanics, you might consider designing a much lower-cost engine that runs for a short mission life and then throw it away,” Stagney said.
A customer-focused approach has been the key to GATORWORKS, which formed in 2018 to focus on the “rapid and agile development” of military engines. Instead of beginning a project with hundreds of requirements, the idea is to focus on the customer’s top three priorities. Those requirements go to a small design team, which builds and tests each iteration quickly, with the freedom to innovate and experiment.
GATORWORKS currently has a pipeline of highly innovative new products in various stages of development and recently demonstrated the ability to deliver new capabilities in half the time of a traditional development cycle through the use of agile and digital techniques.
“We’ve got teams that are really excited and empowered because we give them the flexibility and authority to solve problems in a different way,” Stagney said.
They too, no doubt, will break new barriers and broaden the technical boundaries of propulsion.
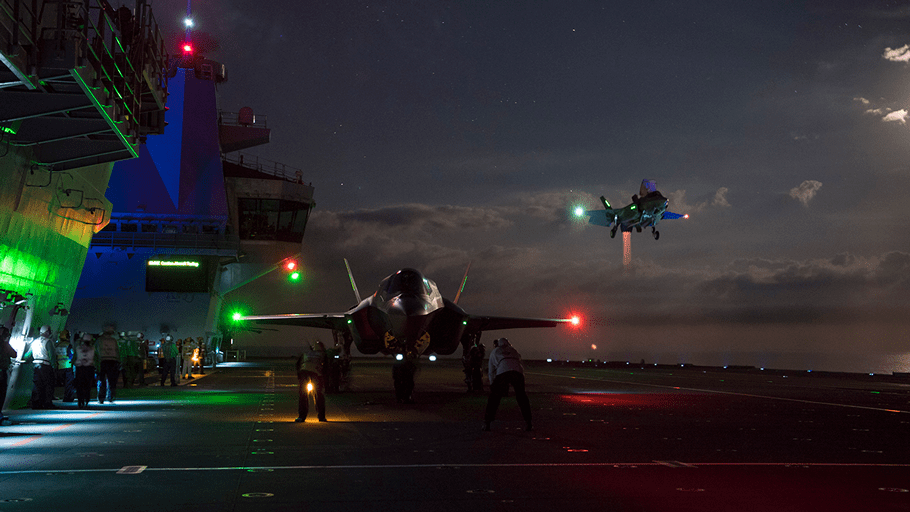