Got a problem? Give it to an engineer.
RTX engineers take on tough problems across aerospace and defense
When you get right down to it, all engineers have the same basic job description: They solve problems.
It doesn’t matter where they work, or in which discipline. Aerospace engineers, software engineers, electrical engineers, systems engineers – they all find ways to make things work to a set of requirements and despite the constraints of the physical world.
And while what they design is often fascinating, how they got there can be just as interesting – particularly at a company like RTX, where engineers work every day to push the limits of aerospace and defense technology.
Here, engineers from across the company walk through some hard problems they’ve solved, and how they did it.
Circuit breaker breakthrough
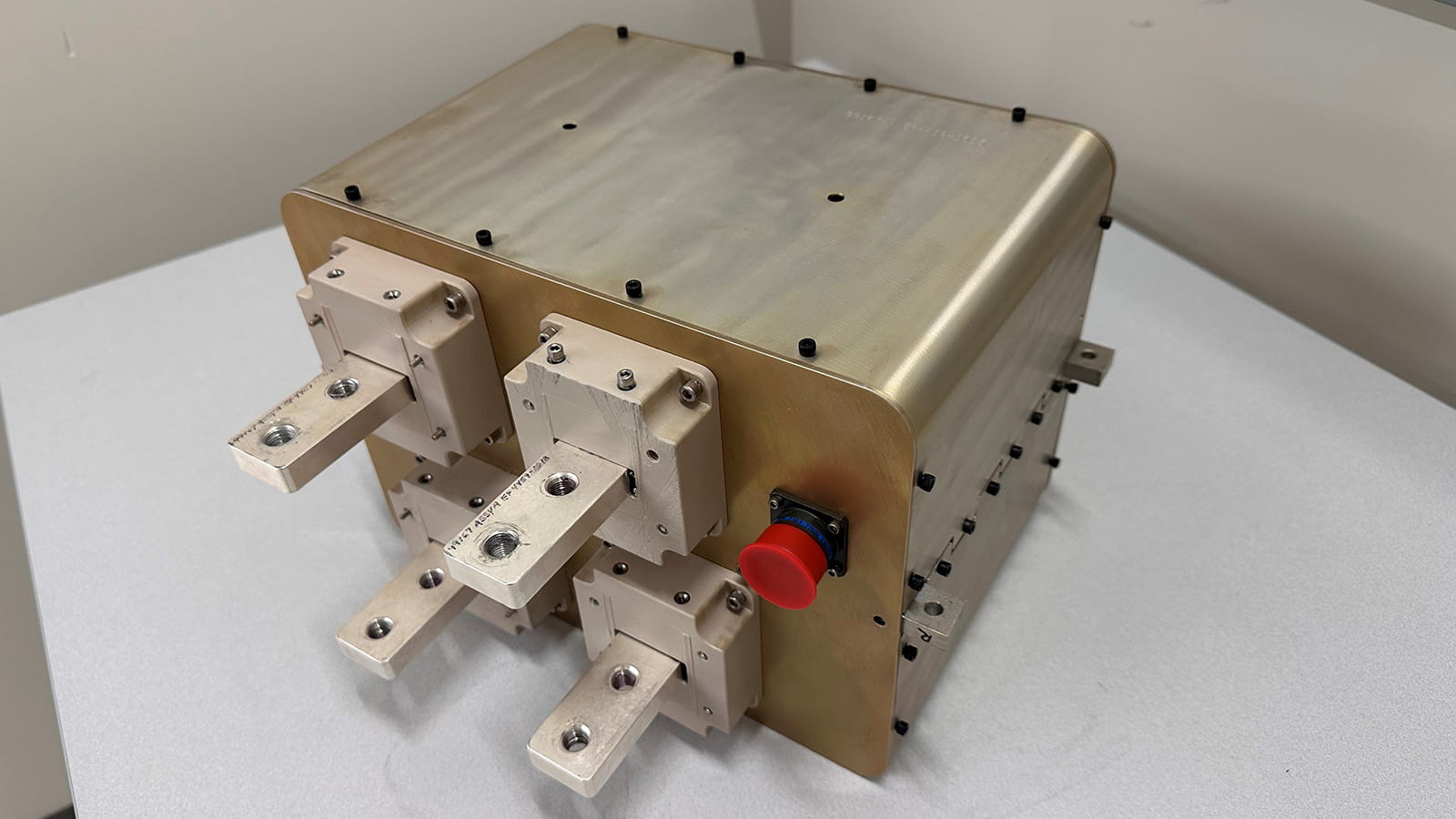
“On an electric aircraft, the power output is much higher ... the circuit breaker needs to be right-sized to keep up.”
Josh Swenson | Senior Technical Fellow | Collins Aerospace
Circuit breakers are the unsung heroes of any electrical system. As first responders to trouble – a failure, spark or other potential danger – their job is to shut off the flow of electrical current quickly when the systems they protect are at risk.
The higher the voltage, the more powerful the circuit breaker. Build onto your house, and you’ll need a circuit breaker upgrade to handle the added electrical load. But how do circuit breakers work on a much larger scale, like on an aircraft? What about on a fully electric aircraft?
The problem: Great as they are, the workhorse circuit breakers on today’s commercial aircraft are no match for the voltage and power output that electrified aircraft will require.
“A Boeing 787 has over a thousand solid-state circuit breakers – but only a few dozen that can handle more than 10 amps,” said Josh Swenson, a senior technical fellow and principal engineer at Collins Aerospace, an RTX business. “On an electric aircraft, the power output is much higher, with four or five times as much power. The circuit breakers need to be right-sized to keep up.”
OK, but what happens when the breaker trips? Wasn’t that electricity doing some important work?
Not to worry, Swenson said. Much like today’s dual-engine commercial jets have redundant controls and fuel systems to prevent engines from losing power, electric aircraft will have safeguards including multiple propulsors, energy sources, motors and drives.
“The exact number of redundancies may be different for different aircraft,” he said, “but each will have backup systems to ensure safe landing.”
The solution: Building that right-sized circuit breaker is exactly what RTX engineers did. Through modeling, simulation, and a little help from additive manufacturing, the team created a next-generation circuit breaker that can interrupt thousands of amps in less than 10 milliseconds. That’s five times the power of those flying today.
Case study: When Pratt & Whitney won a contract to provide new circuit breaker technology as part of NASA’s Advanced Air Vehicles Program, they turned to colleagues at Collins Aerospace and the RTX Technology Research Center for help.
The center took the lead on design, and its power electronics and additive manufacturing teams served in testing and advisory roles, while engineers from Collins in Germany worked on the control board and software. A Collins team in Rockford, Illinois, was responsible for thermal regulation and packaging.
Conundrum and compromise
One of their early hurdles was circuit breaker response time.
“The higher the voltage, the more challenging it is for traditional, metal-based mechanical switches to stop the flow of current,” Swenson explained.
That’s because of an air gap inside the switch that can arc, or spark over, when overtaxed, posing a fire risk and damaging the switch. In other words, when voltage is too high, it can override the switch that’s trying to control it.
A silicon-based, solid-state switch has no moving parts, so there are no air gaps or other variables like springs that can wear out. It’s a good choice for high voltages but creates a new challenge: heat.
“With every amp you’re conducting, there’s higher resistance to the current,” said Swenson. “That means more heat loss and higher temperatures. We were looking for a compromise – a solid-state, silicon-based conduit that could quickly turn off current while managing all that additional heat.”
Redefining cool
The team looked at existing heat removal systems, called cold-plate heat exchangers, that use fins folded like an accordion to transfer heat to liquid coolant. But standard configurations lacked the surface area to accommodate the increased heat.
That’s when research center engineers suggested additive manufacturing for a custom cold-plate solution.
“Additive manufacturing let us explore new geometries to optimize thermal performance,” said Charles Shepard, principal mechanical engineer on the Collins electronics packaging team. “Fins could be different geometries, orientations and densities rather than the traditional uniform folded or machine fins. The ability to create unique features and use the third dimension opened up design options we haven’t had before.”
Thanks to a culture of problem-solving, RTX engineers worked together to create a heat-regulating, solid-state circuit breaker with the power and potential to advance fully electric flight.
Diamonds: A radar’s best friend
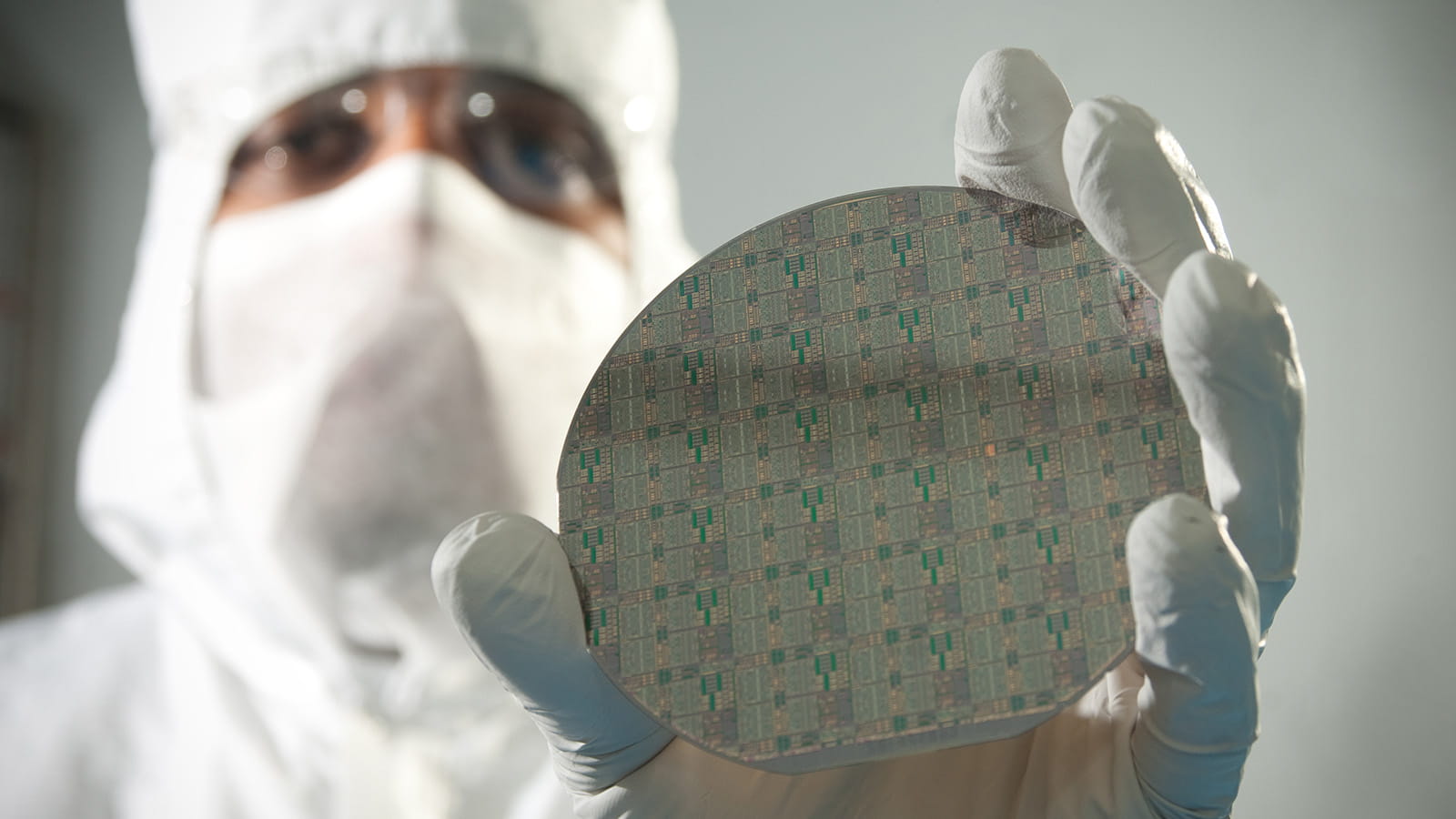
“Diamonds could revolutionize radars in military aircraft, ships, drones and air defense systems. The sky is the limit.”
Matt Tyhach | Senior Technology Fellow | Raytheon
Gallium nitride is a powerful semiconductor that Raytheon uses in the circuitry of its radar systems to boost their signal strength. The business pioneered the use of the glasslike material, also called GaN, in the early 2000s and has successfully used it in large land- and sea-based radars, as well as the smaller radars on fighter jets.
The problem: You can’t just put gallium nitride on any ordinary circuit card – and if you did, you wouldn’t be able to take full advantage of it. Gallium nitride, like any semiconductor, gets hot as more power flows through. And it can get very, very hot.
“GaN generates so much heat that we have to throttle back its performance, so it doesn’t overheat a transistor,” said Matt Tyhach, who leads next-generation sensors and microelectronics in Advanced Technology at Raytheon, an RTX business.
Tyhach faces a classic engineering problem: How do you dissipate heat quickly, so that you can dial up the energy to increase a radar’s power and sensitivity?
The solution: It involves materials science, physics, thermal, mechanical and electrical engineering, and the world’s best thermal conductor – diamond.
Tyhach, working with his colleagues across Raytheon, government and industry, is using lab-grown diamonds to pull away heat from GaN transistors.
Today’s transistors are grown on a substrate of silicon carbide, a good thermal conductor. But diamond, Tyhach said, offers five times the conductivity of silicon carbide, “so it can wick away heat from a transistor much faster.”
Magic, or just science?
He even has a bit of a magic trick to demonstrate diamond’s superb thermal conductivity. Sometimes at career fairs, he’ll pick a piece of ice from a cooler, then touch it with a lab-grown diamond – cutting through the ice effortlessly as the diamond transfers heat from his fingers.
That’s great, but applying the principle to radar systems presents another challenge: How to turn that lab-grown diamond into a workable substrate. As Tyhach explained, you can’t just stick it on a transistor. Diamond has to be polished with other diamond before bonding, and the bonding only works if the layer you’re attaching is microscopically thin – a nanometer or less.
Placing diamond underneath and on top of a transistor unlocks new possibilities for GaN, where thermal management is no longer a limiting factor, Tyhach said.
“We can dial up the voltage, dial up the power density and get more out of our systems,” he said.
Cost is the main challenge, but the future of this technology looks promising.
“The same companies that make artificial diamonds for jewelry are also making them now for semiconductors,” Tyhach said. “There will always need to be a commercial pull to bring the price down … adjust the volume, supply and demand.”
The case study: Raytheon is integrating lab-grown diamonds right next to the hotspot, its military-grade GaN transistor. The upgraded device will boost radar output power and sensing ability by 16 times without exposing the components to a rise in temperature.
“We’re giving our systems more sensitivity to find and track both smaller and more objects within the same range,” Tyhach said.
The prototyping work is being done under a DARPA program called THREADS, or Technologies for Heat Removal in Electronics at the Device Scale.
Raytheon is partnering with the Naval Research Laboratory, Stanford University and Diamond Foundry to grow diamond, while various universities analyze technology and performance.
Collaborating with that team has been a reward in itself, Tyhach said.
“I get to work with some of the brightest technical minds in the industry,“ he said, “and we’re taking this technology from concept into reality.“
Integration, along with electrical, thermal and reliability testing, will be done at Raytheon’s GaN foundry in Andover, Massachusetts, which also produces GaN for many of its other defense systems.
“Diamonds could revolutionize radars in military aircraft, ships, drones and air defense systems,” Tyhach said. “The sky is the limit.”
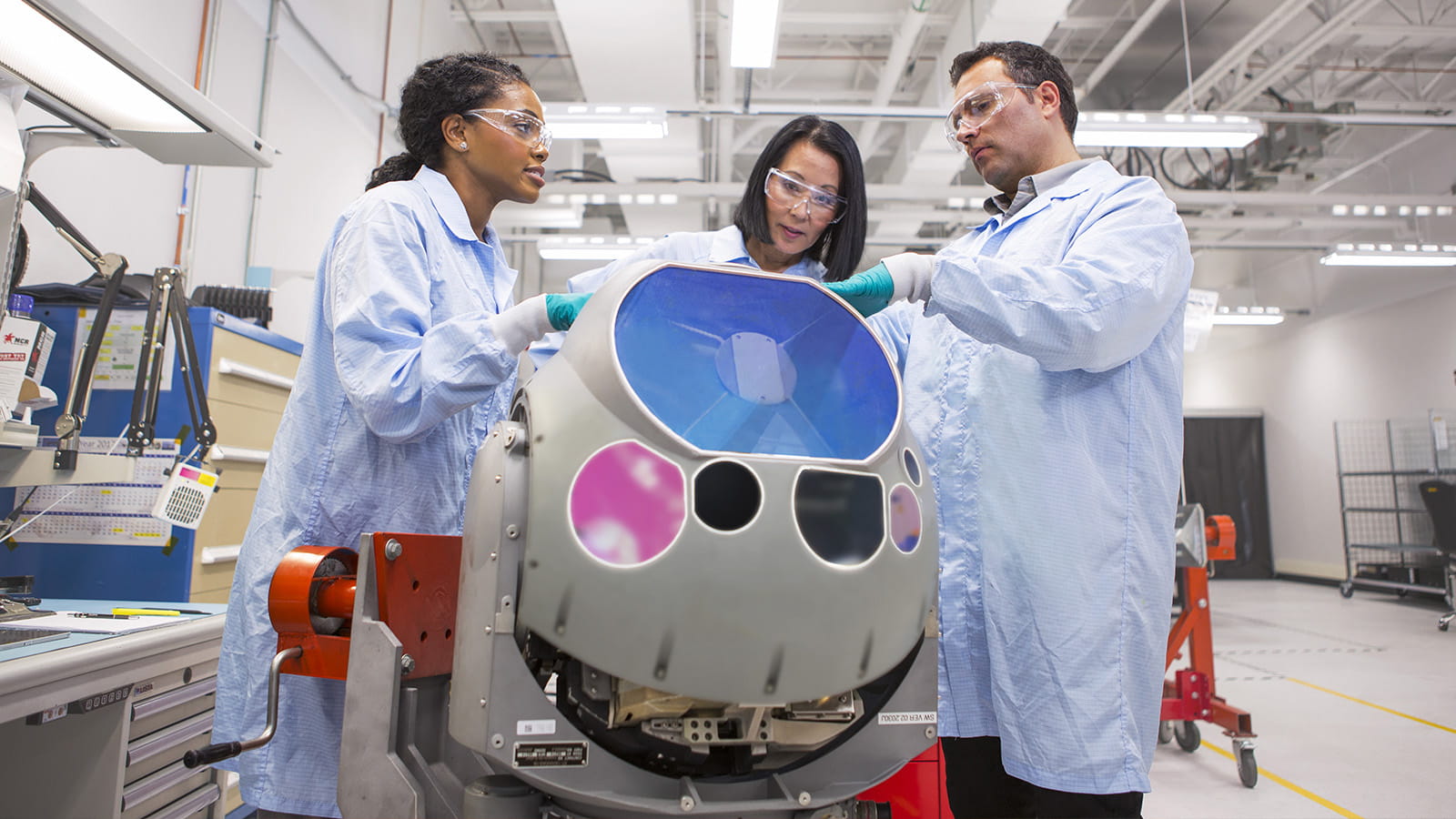