Digital transformation: How Raytheon Technologies is finding ways to work smarter and faster
The torque wrenches at a new factory tell technicians exactly when to stop turning. A computing cloud allows engine experts across the world to collaborate on compressors, combustors, intakes, exhausts and all the other parts that help aircraft take flight.
A data analysis system prevents flight delays by predicting the optimal time to replace parts on planes. And a “digital twin” of a new missile defense radar has helped engineers build the real thing far faster than older methods ever would have allowed.
Raytheon Technologies employees around the world are in the midst of a “digital transformation,” finding new ways to deliver, maintain and improve products quickly, reliably and efficiently – all part of the company’s broader initiative to optimize its operations and add value for customers.
“Digital transformation is a team sport. This is multi-disciplinary. It touches every part of the company,” said Vince Campisi, the company’s chief digital officer.
Rethinking the prototype
Digital technologies offer significant advantages in product design. New, all-digital methods of modeling and simulation allow engineers to build precise, accurate 3D models of their designs, then plug in real-world data to see how those designs perform in specific situations.
That method is far faster and less expensive than building a traditional prototype and taking it to a physical test range, and it allows product teams to test as much and as often as their computers can handle.
In one case, the developers of a new air-launched cruise missile have been flying their digital design 6 million miles every night, generating troves of test data that would be impractical to replicate in the real world.
“We fly it every night and we learn. We learn how it performs against various threats, how it works in different environments,” said Bryan Rosselli, vice president of Business Transformation & Execution at Raytheon Missiles & Defense, a Raytheon Technologies business. “If the customer wants to try a different threat scenario, we can model it instead of having to do a costly flight test. It vastly accelerates not just the development process, but the learning you can do.”
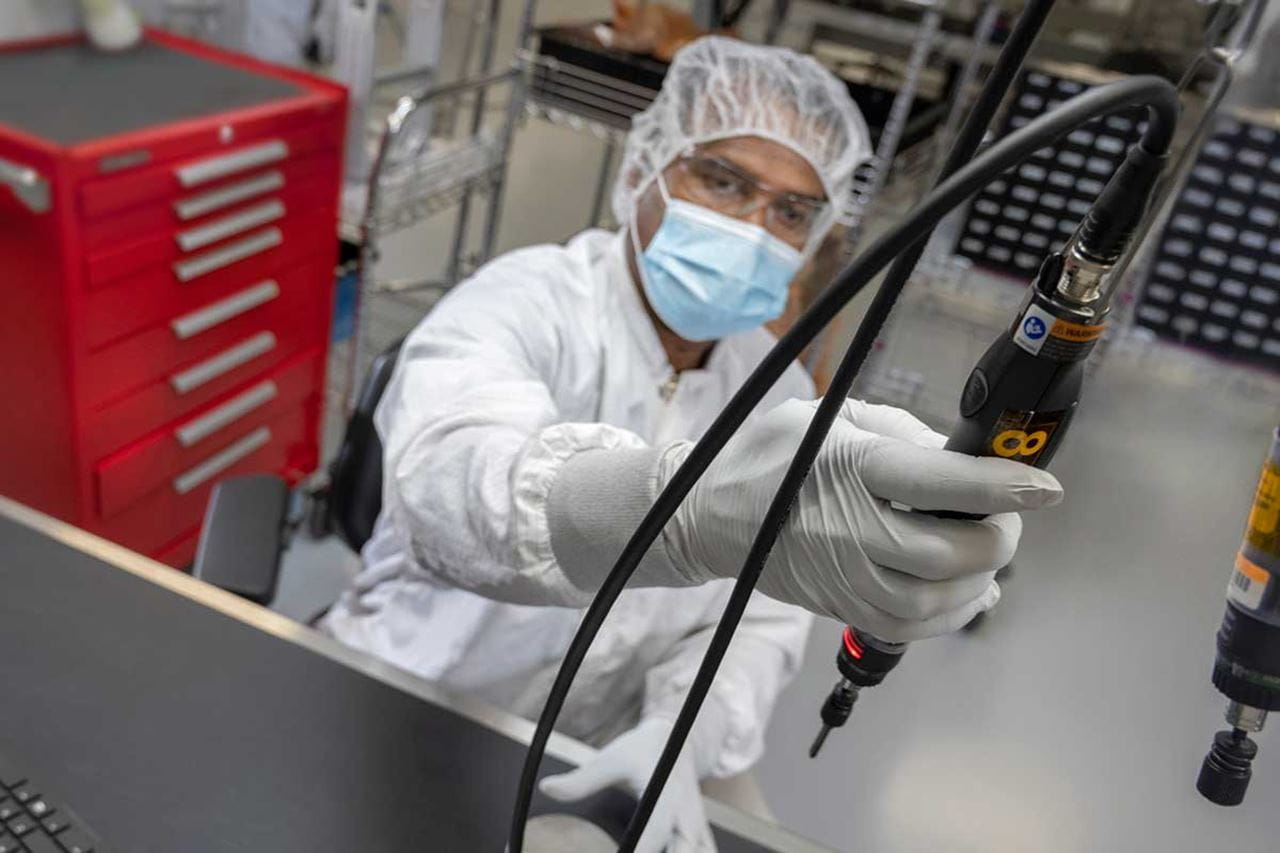
An operator reaches for an automated torque tool at Raytheon Intelligence & Space's Advanced Integration & Manufacturing Center in McKinney, Texas. The facility features new automated tools preprogammed with assembly instructions to streamline operators' workflows.
Factories as data consumers – and sources
Digital transformation continues on the factory floor, where Raytheon Technologies is working to link about 20,000 pieces of manufacturing equipment to its networks.
The vision, according to Senior Vice President for Operations & Supply Chain Paolo Dal Cin, is a data repository employees can consult for deep, detailed, on-demand knowledge of the work happening across the company’s 200 manufacturing facilities.
“That, for me, is where you start to really be able to scale,” he said. “The designers can go look for information on the parts they’re working on and see how they’re being produced almost in real time, or how they were produced as you look back in time. And the people in the field supporting the products could see exactly how they were produced.”
The value of data sharing extends to suppliers, Dal Cin said. It enables better coordination by allowing the company to ensure suppliers are producing at the right levels months in advance; it would help suppliers anticipate demand for parts, and it would flag potential production problems earlier, giving both parties a better opportunity to address them.
“Ultimately, we want to be able to see not a commitment on when they’re going to deliver a part, but rather that they have enough material in process to cover our needs over the next four to six to eight to 36 weeks,” Dal Cin said.
Beyond that, data can pay huge dividends for products already in the field. Predictive analytics allows the company to monitor products currently in use and advise customers on when to replace them to avoid service disruptions.
“Our ability to monitor performance of products in service allows us to identify trends they might not see otherwise,” Dal Cin said, “which would, in turn, allow us to engage with them or their customer to identify a need and improve performance.”
A driver of employee satisfaction
Another goal of Raytheon Technologies’ digital transformation: to help employees thrive.
That includes widespread use of data clouds and real-time remote collaboration tools, as well as advanced manufacturing technologies like automatic data entry and smart workstations.
Those approaches have already sped up production cycles – by 30 percent in some cases, Campisi said – and the benefits will only grow as the new methods take hold. And faster production means greater employee satisfaction, Campisi said.
“Job candidates want to join a company that’s on an amazing mission, which we all believe and know we are, and they want to see the work they contribute get fielded in a reasonable amount of time,” Campisi said. “Other industries have demonstrated that. We have the ability to demonstrate it too, and when we do, the value it can unlock is great.”
In the long term, Campisi said, he looks forward to the day employees go beyond thinking of the new methods as novel or extraordinary.
“Ultimately, you don’t want to have pathfinder programs that are teaching people to work differently,” he said. “You just want it to be Thursday, and that’s how everybody is working on every program.”