Poised for a future of hydrogen-powered planes
In projects unfolding across RTX, researchers advance hydrogen as a powerful, transformative aviation fuel
Standing in a control room and looking through a pane of glass, Lance Smith had his eyes fixed on the blue flame coming out of a test aviation rig in the next room.
For hours, natural gas had been flowing into a combustor in a facility at the RTX Technology Research Center in East Hartford, Connecticut, that simulates the heat and high pressure of an engine. Smith gave the signal for a test engineer to flip the switch, then watched the flame change instantly to a glowing orange red.
And that was the confirmation he needed. For the first time, hydrogen was powering the test combustor – a major development in a Pratt & Whitney project known as HySIITE, or Hydrogen Steam Injected, Intercooled Turbine Engine.
“It’s one of these rare times you get to see something that’s really new,” said Smith, an RTX senior technology fellow. “But then you knuckle down and make sure it’s right.”
And it was. Smith and his team checked and re-checked the data and the HySIITE test showed “you can burn hydrogen, clean,” he said.
“You can burn it safely and robustly. You’re not going to burn up the combustor, but you can take this explosive, highly flammable gas and put it in a combustor and burn it safely and stably. And it comes in a package that is super efficient. The takeaway is there’s a solution here.”
The results of Pratt & Whitney’s HySIITE program – sponsored by the U.S. Department of Energy’s Advanced Research Projects Agency-Energy – show RTX is advancing technologies that will allow the aviation industry to use hydrogen at scale. The project is unique because it is optimized for liquid hydrogen, capturing water from the engine exhaust to enable improved efficiency and reduced nitrogen oxide (NOx) emissions. It is among several projects unfolding across RTX as the company taps into both its commercial aviation businesses and its research-and-development capabilities to advance hydrogen as a powerful, efficient and transformative aviation fuel.While the HySIITE program wrapped in December 2024, RTX is underway on two other new projects to drive the future of hydrogen in aviation: the Hydrogen Advanced Engine Study (HyADES), a program supported by Canada’s INSAT (Initiative for Sustainable Aviation Technology), which advances the use of hydrogen for turboprop aircraft; and COCOLIH2T, which is focused on creating a way to store fuel aboard aircraft and is supported by the European Union’s Clean Hydrogen Joint Undertaking.
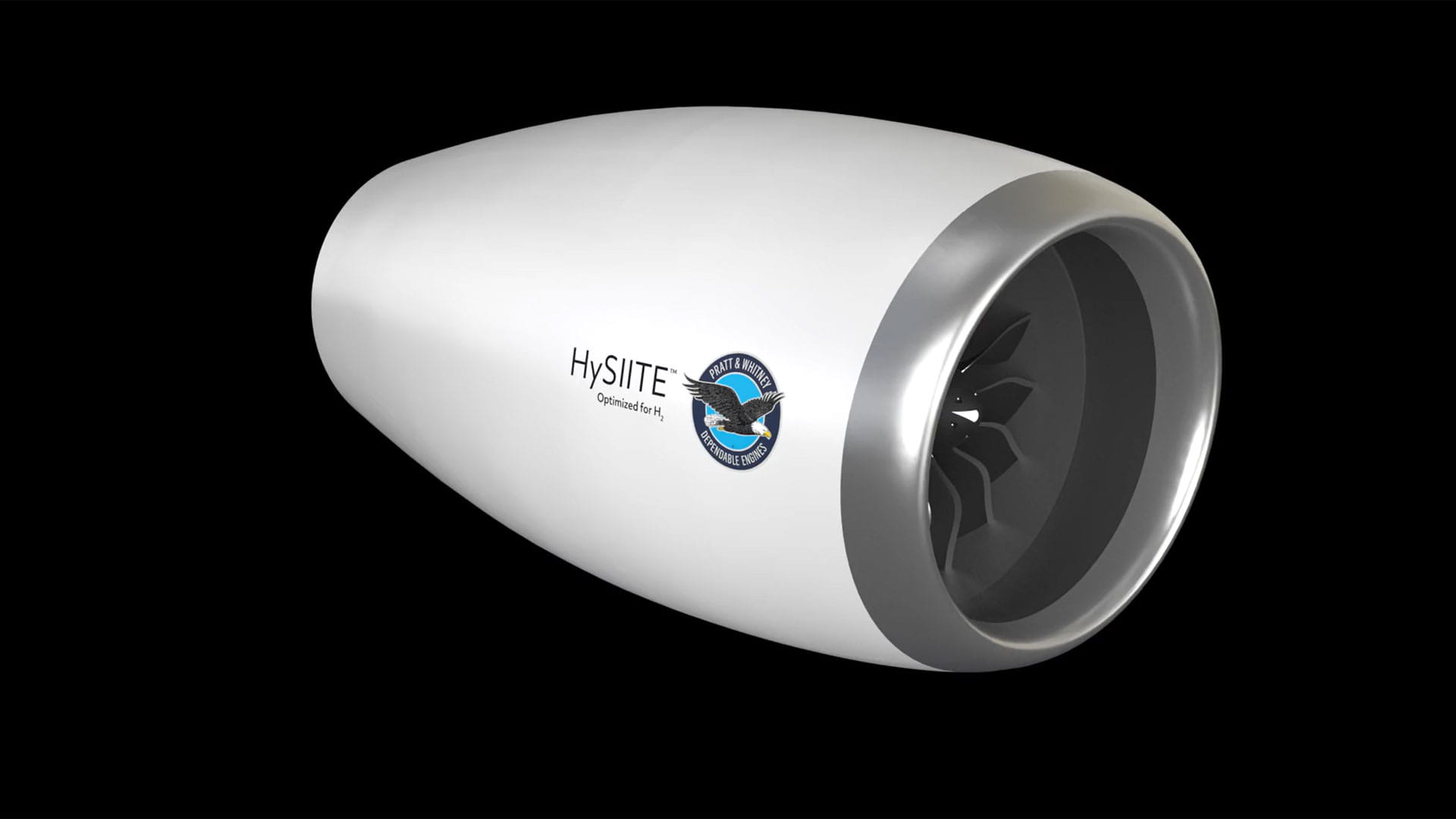
The results of Pratt & Whitney’s Hydrogen Steam Injected, Inter-cooled Turbine Engine (HySIITE) rig test – sponsored by the U.S. Department of Energy – show RTX is advancing technologies that will allow the aviation industry to use hydrogen at scale. The project is among several unfolding across RTX, as the company taps into both its commercial aviation businesses and its research-and-development capabilities to advance hydrogen as a powerful, efficient and transformative aviation fuel.
The HySIITE rig tests delivered or exceeded performance expectations. Highlights include:
Take on the hard part first
The company’s successful HySIITE tests and work in this space show that hydrogen has the potential to become a commonplace – and powerful, efficient – aviation fuel.
“We are understanding the value,” said Michael Winter, chief scientist at RTX. “HySIITE is the most realizable architecture for the future of hydrogen fuel and propulsion at scale. If hydrogen becomes widely available, Pratt & Whitney will be ready for that future.”“Whatever new technologies we bring forward, they need to be more safe than anything flying today and they need to provide better customer value,” he continued. “If I had an engine that was 35% more efficient, that translates into a dramatic savings for our customers, the airlines, and the air force of our nation and our allies.”
Winter said this result was achieved at Pratt & Whitney and RTX because of the company’s engineers - who learn to “take on the hard part first and understand it is going to work.”
“One of the approaches that this demonstrates is agile technology development,” said Winter. “We choose the hardest technology challenges and we actively choose to demonstrate those first.”
A low roar
In the control room next to Smith, Jacob Snyder was on his third day testing another part of the HySIITE program – the rig’s evaporator. Snyder, a principal engineer at Pratt & Whitney, and his team needed to demonstrate it could survive in the exhaust of the jet engine for the life of the engine.
“It was like a low roar – a bit like being in a plane – that low roar of the air rushing past,” Snyder remembers of the testing room. “There was a non-zero chance this thing would explode. When it survived the testing with flying colors, there was a big sense of relief. I was monitoring temperatures of the streams of water and air going in and making sure they were within the range we were expecting. These parts are under a significant amount of thermal stress – they are taking basically room temperature water and heating it up so you have a large temperature gradient. There is always a bit of uncertainty.”
“The fact that all the tests came back better than expected really made us think this technology could be a viable option for the future of hydrogen,” he continued.
The work continues
John Hu is a combustion technology manager at Pratt & Whitney Canada working on the HyADES program, which launched in January 2024. That project demonstrates hydrogen in an existing PW127XT turboprop engine, and in doing so could provide a nearer-term advancement.
“There is a lot of talk about hybrid and improving engine efficiency, and we see that it’s a multi-prong approach so we want to be ready,” said Hu. “We have to be in front of our customer and ready.”
A whole new concept
For Smith and Snyder, the moment they saw their HySIITE tests worked felt monumental – for the industry and for them.
“There are a handful of times in your career when you do something new and exciting and this is one of them,” said Smith. “It’s not that often you get to try out a whole new concept. At the end of a career, that’s a highlight. That’s an accomplishment you carry with you.”
Acknowledgment: The information, data, or work presented herein was funded in part by the Advanced Research Projects Agency-Energy (ARPA-E), U.S. Department of Energy, under Award Number DE-AR0001561. The views and opinions of authors expressed herein do not necessarily state or reflect those of the United States Government or any agency thereof.