Raytheon Technologies’ former companies had long-standing histories of excellence in Environment, Health & Safety (EH&S). Building on their best practices, we have created a set of EH&S principles, a management system and sustainability goals.
EH&S principles
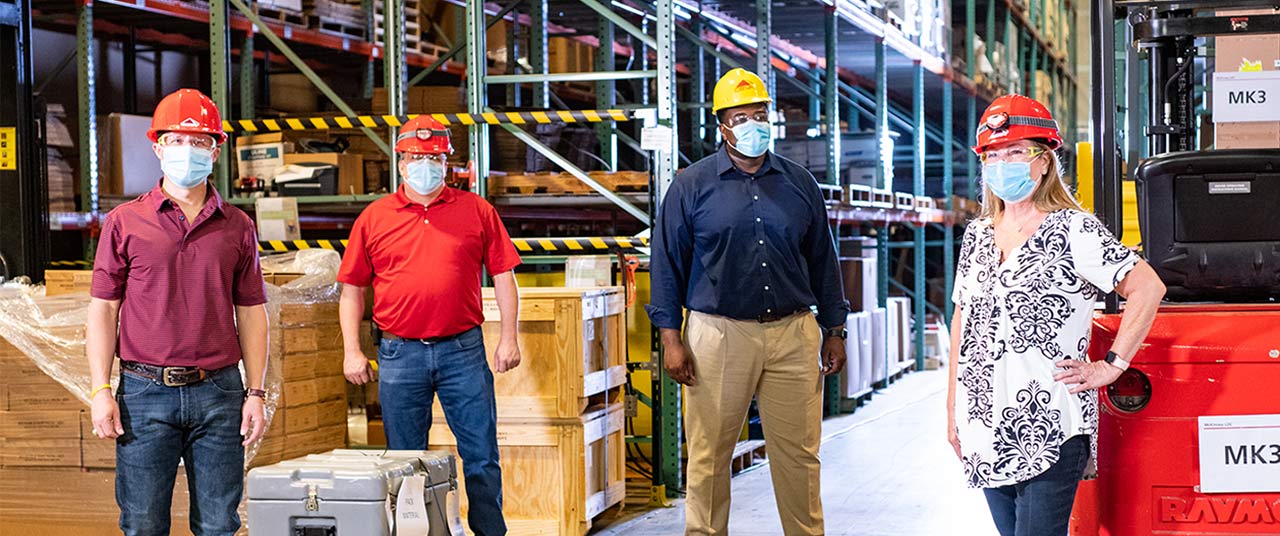